Multi Head Packing Machine
What is Multi Head Packing Machine?
The multi head packing machine is actually a multi head packing line, because it includes a variety of different equipment.
Weighing and packaging are the most important processes of a multihead weigher packing machine, the multihead weigher is responsible for weighing, and the VFFS machine is responsible for packaging.
The weigher packing machine can not only accurately weigh the products, but also automatically package the weighed products, it is very efficient and easy to use.
In fact, the weigher packing machine can complete a series of processes in one stop, such as:
- Material Feeding
- Weighing
- Bag Making
- Material Filling
- Bag Sealing
- Date Code Printing
- Packed Pouch Outputting
Packable Products
It is capable of packing many products in the food, pharmaceutical, daily chemicals, electronics, hardware industries.
- Food
Puffed food, potato chips, candies, pistachios, raisins, glutinous rice balls, meatballs, peanuts, biscuits, jelly, candied fruit, walnuts, pickles, frozen dumplings, almonds, salt, sugar, red dates, oatmeal, etc.
- Pharmaceutical & Chemical
Fertilizer pellets.
- Daily Chemical
Washing powder.
- Hardware
Screws, nuts, fasteners, nails.
Factors to Consider in Purchasing
When you plan to purchase a weigher packing machine, you’d better understand the following information.
Keep the following information in mind, you can find the most suitable model, and save priceless time and energy.
- Product Type
You must clearly know the product you want to pack, know the product’s sizes, and take some clear photos of the product.
These clear photos can help suppliers quickly figure out a suitable machine.
- Pouch Type
Common pouch types include: pillow pouch, 3 side sealing pouch, 4 side sealing pouch, gusset pouch, stand up pouch.
- Pouch Material
Common materials for pouches are composite film, anti-static film, matte film, aluminum foil film, printed film, non-woven fabric, etc.
- Pouch Thickness
It is the pouch material’s grammage, which refers to the material’s weight per square meter.
- Pouch Size
With reference to the following photo, pouch size actually refers to the pouch’s total width and total height.
Multihead Packing Machine Schematic
The following photo is the multihead packing machine’s schematic:
The standard multihead weigher packing machine mainly includes the following equipment:
- Vibrating Feeder
- Z Bucket Conveyor
- Multi Head Combination Weigher
- Support Platform
- Vertical Form Fill Seal (VFFS) Machine
- Outfeed Conveyor
Some customers will install a gravity fall metal detector under the head weigher’s discharge chute, remove the detected metal from the waste outlet.
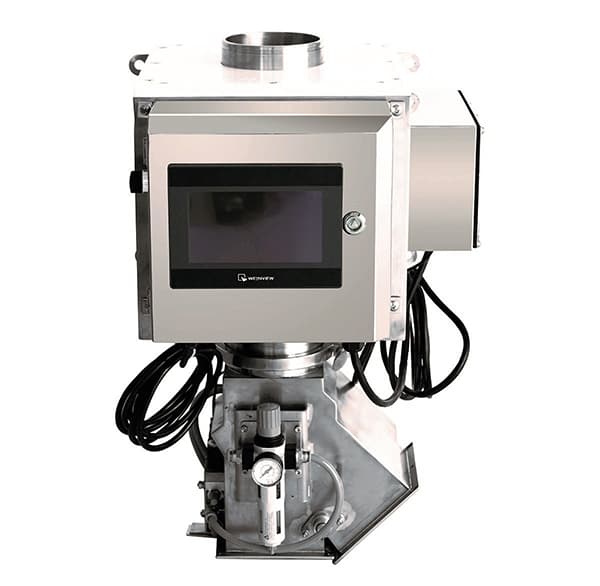
Gravity Fall Metal Detector
In addition, there are some options on the vertical form fill seal packaging machines, mainly including:
- Inkjet Date Coding
It is able to print batch & date codes on the pouch.
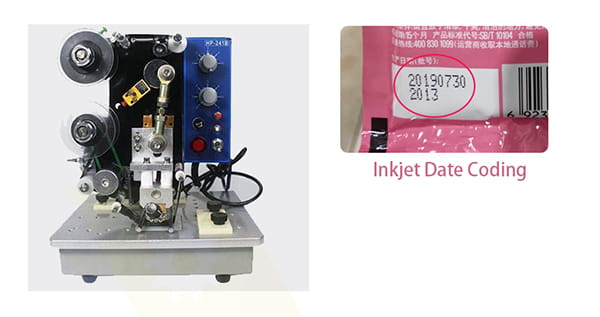
Inkjet Date Coding
- Nitrogen Flush
It is capable of filling nitrogen gas into the pouch, thus removing the oxygen from the food pouch, protecting the food inside for a longer period.
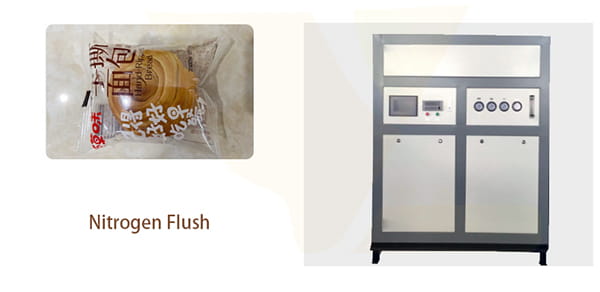
Nitrogen Flush
- Tear Notch
It can punch a notch on the pouch’s top, then customers can easily tear open the pouch.
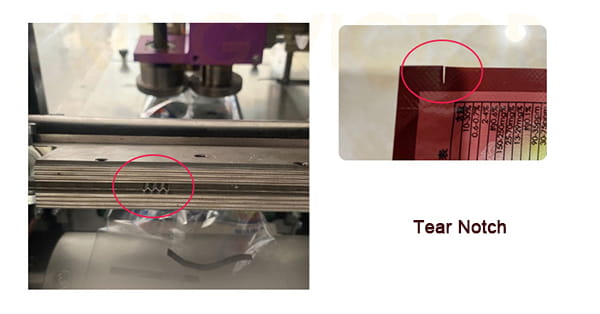
Tear Notch
- Perforator
It can perforate a row of holes while sealing the pouch.
After perforating, several pieces of neighbor pouches link together, thus continuous/chained pouches appear in your eyes.
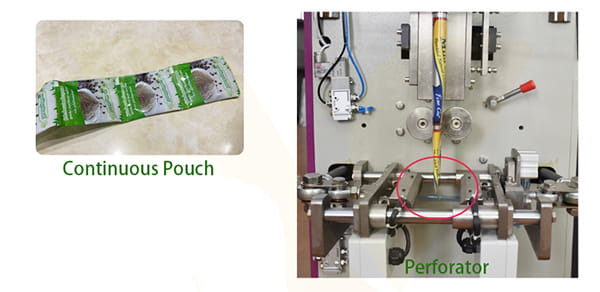
Perforator
- Hole Punch
It can punch a small hole in the pouch, with this small hole, the pouch can hang on the shelf easily.
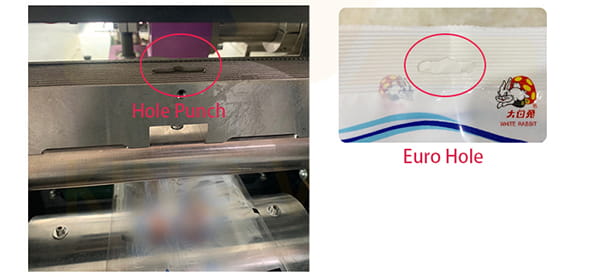
Hole Punch
Working Principle of Multihead Weigher Packing Machine
To better understand the multihead weigher packing machine’s working principle, please refer to the following schematic diagram.
The multihead weigher packing machine’s basic workflow is:
- Material Feeding
- Weighing
- Bag Making
- Filling
- Sealing
- Date Coding
- Discharging
- Checkweighing
- Cartoning
Next, let me introduce the multihead weigher packing machine’s working principle in details.
Material Feeding
Generally speaking, the upstream equipment transports materials to the hopper automatically, or workers manually add materials to the hopper.
The materials in the hopper directly fall onto the feeder, the feeder vibrates the material into the infeed conveyor’s buckets.
The infeed conveyor lifts the material upward, and then dumps the material into the multihead weigher’s infeed chute.
Weighing
A multihead weigher is responsible for weighing.
The materials enter the multi weigher’s dispersion feeder from the infeed funnel.
The dispersion feeder vibrates the material to each radial feeder, and the radial feeder vibrates the material to each pool hopper.
Once the last weighing cycle is over, the material in the pool hopper enters the weight hopper for the next cycle, the weight hopper’s load cell feeds back the measured weight to the PLC.
After the PLC runs the combination calculation, it determines the weight hopper combination, the determined combination is closest to the target weight.
Then PLC sends commands to the corresponding weight hoppers, releases the materials to the discharge chute.
When the timing hopper receives the release command, it will open the discharge chute and outfeed the materials to the VFFS machine’s inlet.
Vertical Form Fill Seal (VFFS)
While the timing hopper is waiting for the command to release the material, the vertical packaging machine starts to work according to the steps of form, fill, and seal.
VFFS Bagger
As shown in the figure below, the vertical packaging machine mainly consists of:
- Film Pulling System
- Former
- Horizontal Sealing Device
- Vertical Sealing Device
- Cutting Device
- Photoelectric Monitoring System
The film pulling system transmits the film to the forming tube, then the film passes through the collar, and two sets of high-quality pulling belts stretch it down.
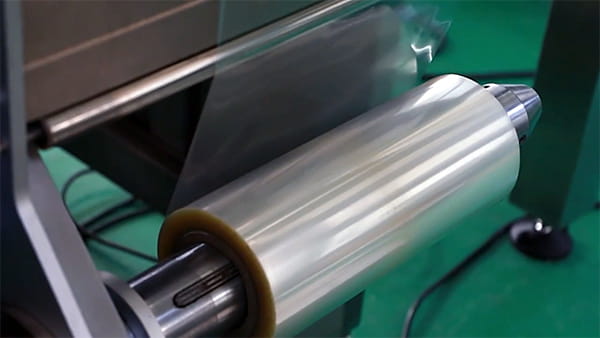
Film Reel
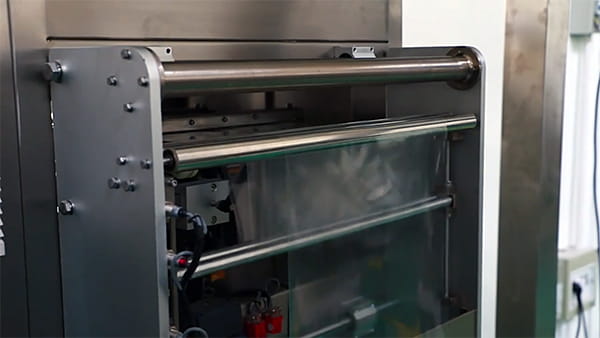
Film Pulling System
When the machine starts at the beginning, the worker manually makes one pouch first, then cuts off the bottom bag, and the upper bag also forms into shape.
During the down-stretching process, the sealed bottom goes down, the vertical sealing bar first melts the vertical edges, bonding the film until the length reaches the preset value.
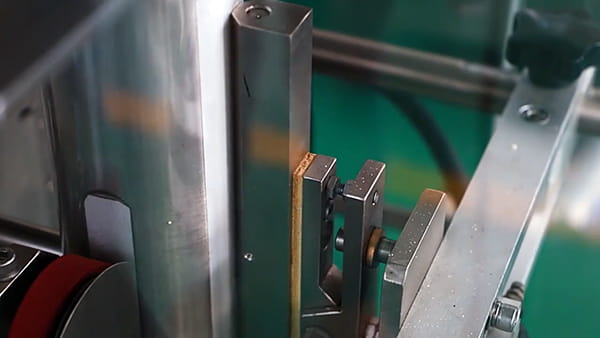
Vertical Sealing Bar
At this time, a top open pouch forms, and the timing hopper releases the material to the open pouch.
After the filling reaches the preset gross weight, the filling stops.
Then the horizontal sealing jaws seal the top of the bag, the upper bag’s bottom forms at the same time.

Horizontal Sealing Jaws
In this way, the pouch forming, filling, and sealing are completed cyclically.
Premade Pouch Filling Machine
If it is a pre made pouch packing machine, the product packaging process mainly includes the following steps:
- Pick-up Doypack
The machine picks up a doypack to the gripper, if the photoelectric eye detects no pouch, the machine sounds an alarm.
In this way, it effectively reduces the labor intensity;
- Print Date Code
Ribbon detection, if the ribbon runs out, alarm pops up on the touch screen, ensure the normal date coding;
- Open Pouch
Open the pouch to detect, if the bag is not open, the machine doesn’t fill material, avoids wasting material;
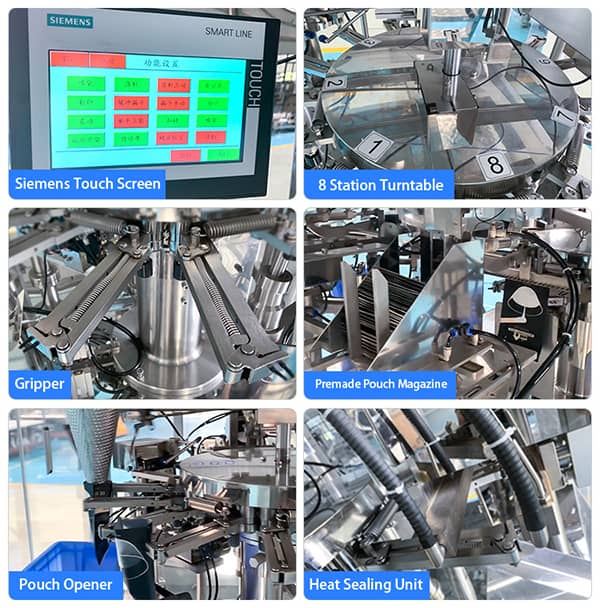
Rotary Pouch Packing Machine
- Fill Material
Inspect first, if no material, no filling and no sealing, avoids wasting bag;
- Heat Sealing
Alarm for abnormal temperature to ensure sealing quality;
- Cooling, Shaping & Discharging
Ensure that the seal is beautiful.
To better understand pre made pouch packing machine’s working process, please watch the below video for reference.
Discharging
After the machine cuts off the pouch from the forming tube, the finished pouch drops directly onto the outfeed conveyor belt, then it forwards to the downstream equipment.
Metal Detection & Checkweighing
Generally speaking, the packed food pouches pass the metal detector first, the metal detector will detect whether the food pouches contain metal.
If detecting metal in a certain food pouch, the pneumatic pushrod will reject it to the waste collection box.
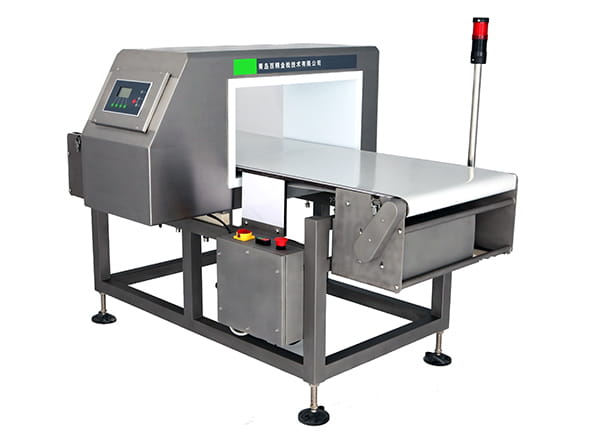
Metal Detector
The qualified food pouches forward to the checkweigher, ensuring the packaging weight is within a reasonable range.
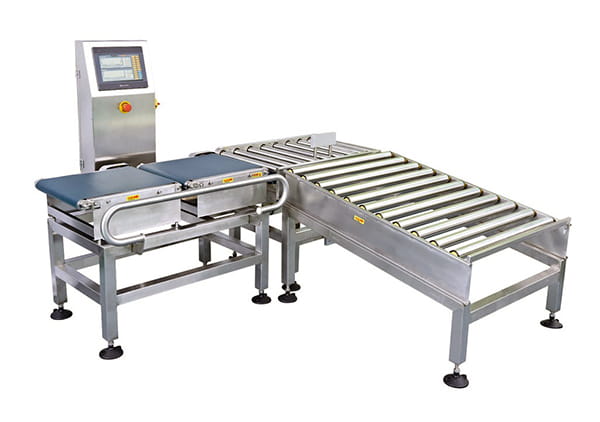
Checkweigher
Some food pouches don’t meet the target weight, their destination is the waste collection box.
Cartoning
After food pouches pass metal detection and checkweighing, they go ahead to the case packer or cartoning machine.
Multihead Packing Machine Features
As the multihead packing machine is composed of many equipment, let’s introduce each equipment’s features one by one.
Vibrating Feeder
A vibrating feeder uses motor vibration and gravity to move materials in a small range, generally distributing materials to a conveyor.
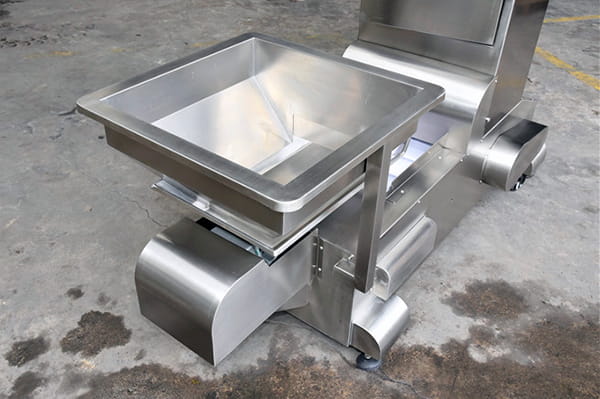
Vibrating Feeder
Vibrating feeders are popular in many industries, including:
- Electronics
- Fast Moving Consumer Goods (FMCG)
- Food
- Hardware
- Pharmaceutical
- Plastics
SiroSilo vibrating feeder mainly has the following features:
- Compact footprint
- Easy installation
- Easy maintenance
- Easy disassembly
- Hygienic design, easy to wash
- Lightly eco-friengly
- Low noise
- Low power consumption
- Speed controllable
- Stainless steel frame
The following table shows the parameters of SiroSilo vibrating feeder.
Hopper Capacity | 140/150L optional |
Conveying Capacity | 3-5m3/h |
Power | 0.3Kw |
Voltage | AC 220/380V |
Frequency | 50/60Hz |
Weight | 105Kg |
Z Type Conveyor
Also known as Z type bucket elevator, lifts the materials from the vibrating feeder to an ideal height, then feeds the materials to the downstream multihead weigher.
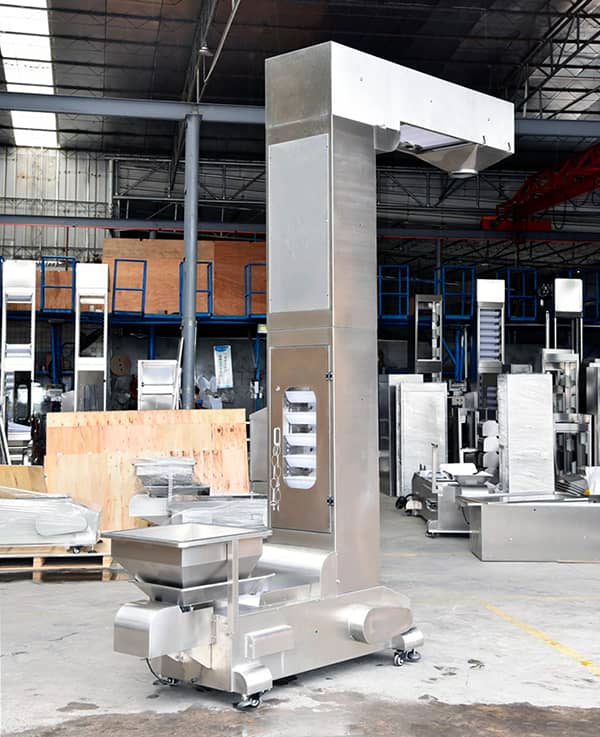
Z Conveyor
The Z type elevator is ideal for conveying many types of food, such as peanuts, soybeans, rice, candy, dried fruits, and other foods.
It often transports granular materials in the daily chemical, hardware, chemical, pharmaceutical, and transportation industries, such as washing powder, screws, nuts, capsules, etc.
SiroSilo’s Z type conveyor mainly has the following unique features:
- All parts with inspection cover or inspection window, quick installation or removal;
- Custom bucket material, SUS304 chain, long service life;
- Built-in chain tensioner and overload protection device;
- Fully enclosed, no spilling, no leaking, no flying dust, clean and hygienic;
- Lifting speed control by invertor, convenient and reliable;
- Powerful sprocket with low noise, stable operation;
- Single-point or multi-point feeding, linkable with various upstream feeding equipment;
- Compact footprint, saves workshop space.
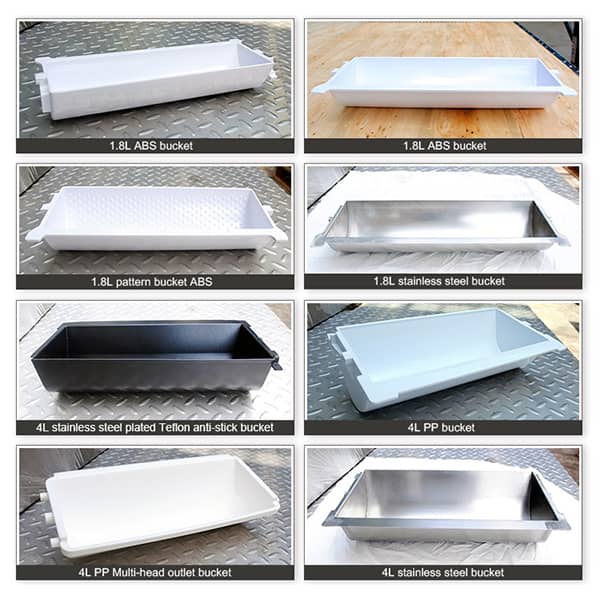
Customized Bucket
Its parameter are shown in the following table.
Conveying Capacity | 4-6m3/h, 6-8m3/h, 8-12m3/h, 12-16m3/h optional |
Voltage | AC220V/380V, 50Hz/60Hz |
Power | 0.75Kw, 1.1Kw-2.5Kw, 3Kw, 4Kw respectively |
Multihead Weigher
The materials lifted by the Z conveyor drop directly into the multi weigher.
After the multi weigher distributes materials to the weigh hoppers, the PLC performs calculations to determine the best weight hopper combination, and this process repeats again and again.
The warranty of SiroSilo multi head scales is two years, its following features are worthy of your attention.
You can also multi head scale to know more details.
Vertical Form Fill Seal (VFFS) Machine
SiroSilo vertical form fill seal VFFS machine can measure and package a large number of granular materials, many customers highly appreciate its following features.
- Parts in contact with materials are made of stainless steel;
- Customizable for different types of pouch styles;
- Double belt driven film pulling system, fast & stable, low friction & loss;
- Highly automated, high production speed & low failure rate;
- Intelligent PID temperature controller, accurate temperature control, beautiful & smooth sealing;
- Parameters setup on touch screen with memory function;
- PLC, servo motor ensures the control accuracy, reliability;
- Safety cover optional;
- The fault display system is helpful for troubleshooting.
To assist you better understanding SiroSilo vertical form fill seal VFFS machine, please watch the following video for reference.
Outfeed Conveyor
The conveying is also realized by the motor-driven chain.
After the vertical form fill seal VFFS machine releases the materials, these materials fall directly into the outfeed conveyor’s hopper.
Rotary Collecting Table
The materials from the outfeed conveyor fall into the rotary collecting table, workers collect and sort them for further case packing.
For the rotary collecting table’s main parameters, please read the below table for reference.
Table Diameter | 1200/1500mm optional |
Voltage | AC220V/380V, 50Hz/60Hz |
Power | 0.37Kw |
Material | 304# stainless steel |
Multihead Weigher Packing Machine Manufacturers
Searching for multihead weigher packing machine manufactureres on Google, most of the SERPs are from India, China, etc.
It indicates that most multihead weigher packing machine manufacturers are located in these two countries.
However, there is also giant multi head pouch packing machine manufacturers, like Ishida.
Ishida invented the first multihead combination weigher, it was founded in 1893, and now it is close to 130 years old.
In addition, there is also a manufacturer of multi head pouch packing machines in the United States, its name is XtraVac.
Multi Head Packing Machine Price
Relatively speaking, many B2B websites broadcast the multi head pouch packing machines’ price in the Indian and Chinese markets.
In the Indian market, the multi head pouch packing machine’s price is about 12Lakh, which is approximately equal to USD$16,188.00;
The multi head pouch packing machine’s price range in the Chinese market is USD$20,000.00-USD$35,000.00.
Multi Head Pouch Packing Machine
Multi head pouch packing machine is actually a packaging line, it is made up of a variety of equipment, multi head weigher and vertical packaging machine are the most important.
According to your requirements of weight range and weighing speed, you can choose 10 head, 14 head, 24 head, 32 head weigher as your like;
According to packing speed, bag type, pouch material, pre made pouch or not, etc., the vertical packaging machine mainly has 2 types:
- Vertical Form Fill Seal VFFS Machine
- Rotary Pouch Packing Machine (Pre Made Pouch Packing Machine)
Among them, the VFFS machine also has 2 types:
- Continuous Motion
- Intermittent Motion
Please feel free to send us an inquiry on this website if you plan to purchase multihead packing machine recently, we will reply to you within 1h.